When Would a Customer Ask Us to Redesign a Gear?
- Share
- publisher
- PairGears
- Issue Time
- Jul 20,2024
Summary
Explore the main reasons customers request gear redesigns — from performance upgrades to cost savings — and how PairGears delivers tailored solutions.
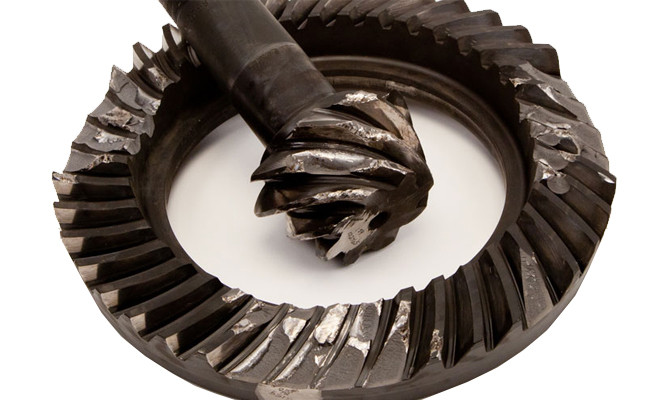
1. Introduction
In the world of mechanical power transmission, gears are the backbone of efficiency, durability, and performance. Yet, no gear design is permanent. Over time, operational demands evolve, industries face new challenges, and machinery needs optimization. This is when customers turn to their trusted gear manufacturer to request a custom gear redesign.
At PairGears, we recognize that every request for redesign reflects a unique need — whether it’s improved strength, reduced noise, or adapting to new environmental conditions. Understanding why a customer might ask for a redesign is the first step toward providing solutions that exceed expectations.
2. Performance-Driven Redesigns
2.1 Increased Load Capacity
When customers increase the output requirements of their equipment, the original gear design may no longer sustain the loads. A redesign can involve stronger materials, optimized tooth geometry, or advanced heat treatment to ensure durability under higher torque conditions.
2.2 Improved Efficiency
Even minor energy losses in gear systems can impact large-scale industrial operations. By optimizing gear profiles and selecting low-friction materials, redesigns can achieve higher transmission efficiency, leading to reduced power consumption.
2.3 Noise and Vibration Reduction
Customers in sectors like automotive and robotics often seek quieter gear systems. Redesigning tooth geometry — for example, shifting from straight bevel gears to spiral bevel gears — can significantly reduce noise and vibration, improving both user comfort and equipment longevity.
Learn more about our Customized Precision Gears.
3. Redesigns Triggered by Failures or Wear
3.1 Frequent Gear Failures
When customers experience repeated breakdowns, it often points to design flaws or unsuitable materials. A redesign can address issues such as inadequate lubrication channels, weak stress points, or fatigue-prone materials.
3.2 Excessive Wear
If a gear exhibits rapid tooth wear, engineers may propose changes in surface treatment, hardness depth, or lubrication strategy. These redesigns not only extend gear life but also reduce maintenance costs
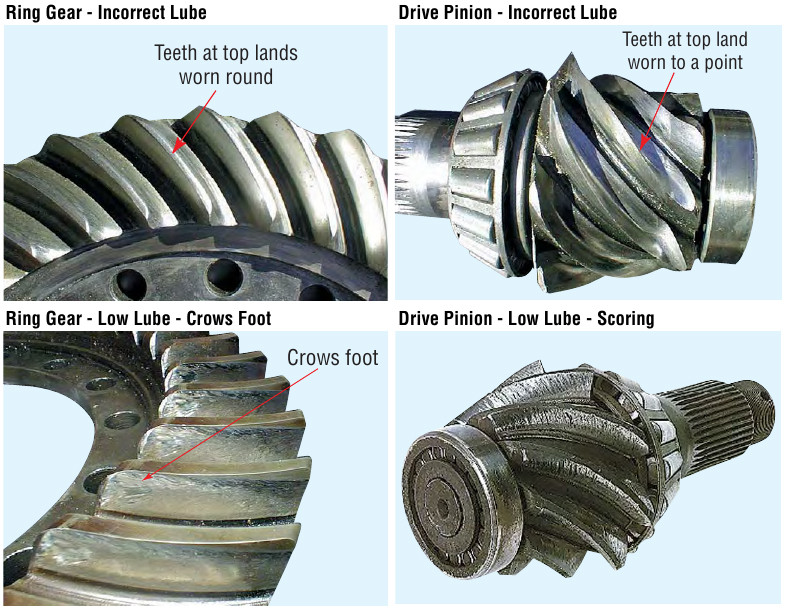
4. Adapting to New Operating Conditions
4.1 Environmental Changes
A gear originally designed for moderate climates may not perform well in high-temperature or corrosive environments. Customers request redesigns with alternative alloys, protective coatings, or seals to handle such challenges.
4.2 Speed and Load Variations
Shifts in operational cycles — such as moving from continuous heavy loads to intermittent high-speed cycles — often require gear ratio adjustments and profile re-engineering.
Reference ISO 6336 Gear Strength Standards: ISO Gear Design.
5. Cost-Reduction Motivations
5.1 Material Optimization
Sometimes customers request a redesign not because of performance issues but to lower costs. By selecting cost-effective yet durable alloys, manufacturers can reduce material expenses while maintaining quality.
5.2 Manufacturing Efficiency
Redesigns can streamline the production process. For instance, modifying the tooth profile for easier machining may cut lead times and improve manufacturability without sacrificing precision.
6. Lifecycle Management
6.1 End-of-Life Scenarios
When a legacy gear design is no longer supported or replacement parts are unavailable, customers seek redesigns to ensure production continuity.
6.2 Product Upgrades
Some customers request redesigns as part of new model launches, where gears must be re-engineered to match upgraded machinery specifications.
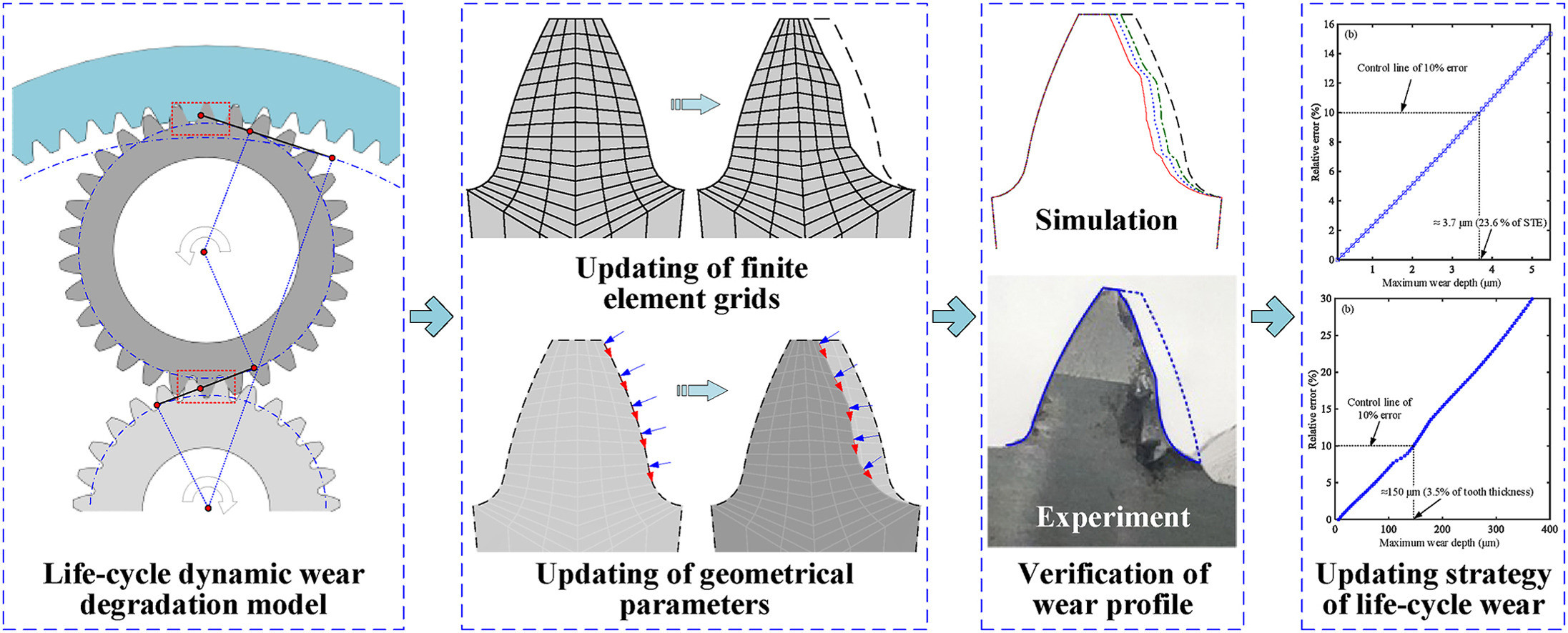
7. Design Optimization Cases
7.1 Weight Reduction
Lightweighting is crucial in aerospace and electric vehicles. A redesign may introduce hollow shafts, optimized tooth counts, or advanced lightweight alloys to reduce system mass without compromising strength.
7.2 Space Constraints
When integrating gears into compact robotics or medical devices, redesigns are often necessary to fit new dimensional requirements.
7.3 Compatibility with New Components
Upgrades in other subsystems often trigger gear redesigns. For example, when a customer adopts a new electric motor, the gearbox gears may need profile modifications to ensure compatibility.
See how PairGears ensures Exquisite R&D and Design.
8. PairGears Approach to Gear Redesign
When customers approach us for a redesign, our process includes:
1. Root Cause Analysis – reviewing the failures or inefficiencies in the current design.
2. Simulation and Testing – using software modeling to predict performance improvements.
3. Material & Process Selection – identifying the best material and treatment combination.
4. Prototype Development – delivering fast-turnaround prototypes for validation.
5. OEM Collaboration – working closely with the client’s engineering team to ensure alignment.
This systematic approach ensures that every redesign not only solves the immediate problem but also adds long-term value to the customer’s system.
Conclusions
A gear redesign is not just about replacing a part — it’s about engineering improvement. Whether driven by performance upgrades, cost reductions, environmental adaptation, or lifecycle needs, customers turn to PairGears for reliable solutions.
By positioning ourselves as a gear engineering partner rather than just a supplier, we ensure that every redesign translates into improved reliability, efficiency, and competitiveness for our clients.Should you have any questions or require further assistance, please do not hesitate to contact our engineer ben@pairgears.com.