The Role of Heat Treatment in Enhancing Gear Performance and Durability
- Share
- publisher
- pairgears
- Issue Time
- Jan 15,2025
Summary
Heat treatment, like carburizing and nitriding, boosts gear performance by enhancing surface hardness, wear resistance, and fatigue strength, crucial for high-quality gears in demanding applications.

Introduction
In the world of gear manufacturing, the ability of gears to perform under stress and resist wear directly impacts the lifespan and reliability of mechanical systems. Heat treatment is a fundamental process that helps achieve these desired properties. By altering the physical and chemical properties of gear materials, heat treatment processes such as carburizing, nitriding, and quenching can significantly improve performance. This blog will dive deep into the importance of heat treatment in enhancing gear performance and durability, with a focus on how PairGears leverages these techniques to deliver superior gear solutions.
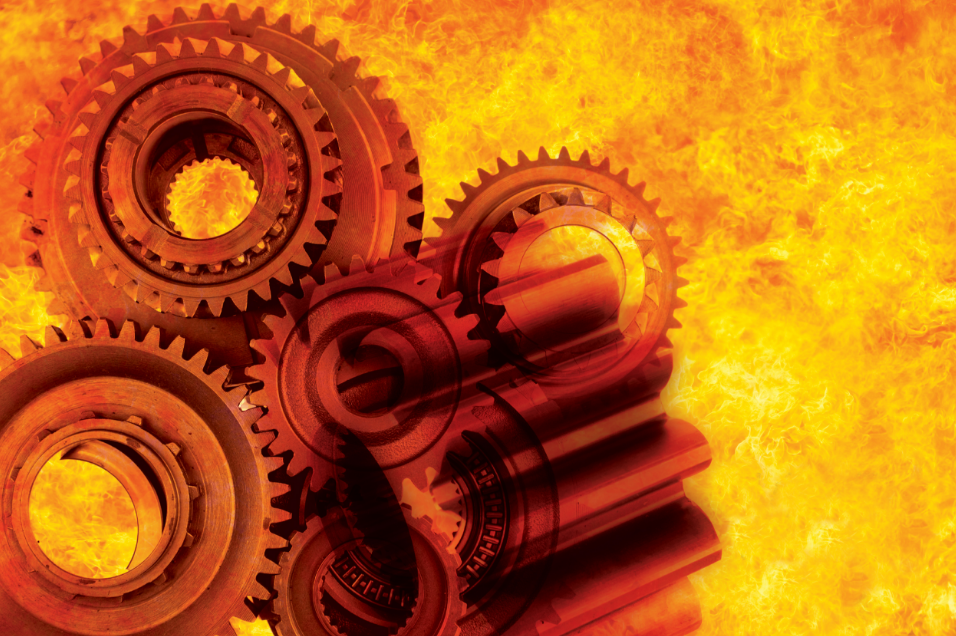
What Is Heat Treatment?
Heat treatment refers to a controlled process in which the gear material is heated to a specific temperature and then cooled at a predetermined rate. This process alters the microstructure of the material, improving its mechanical properties such as hardness, toughness, and strength. For gears, heat treatment not only enhances surface hardness but also improves wear resistance, fatigue strength, and overall operational efficiency.
Common heat treatment processes for gears include:
1. Carburizing
2. Nitriding
3. Induction Hardening
4. Quenching and Tempering
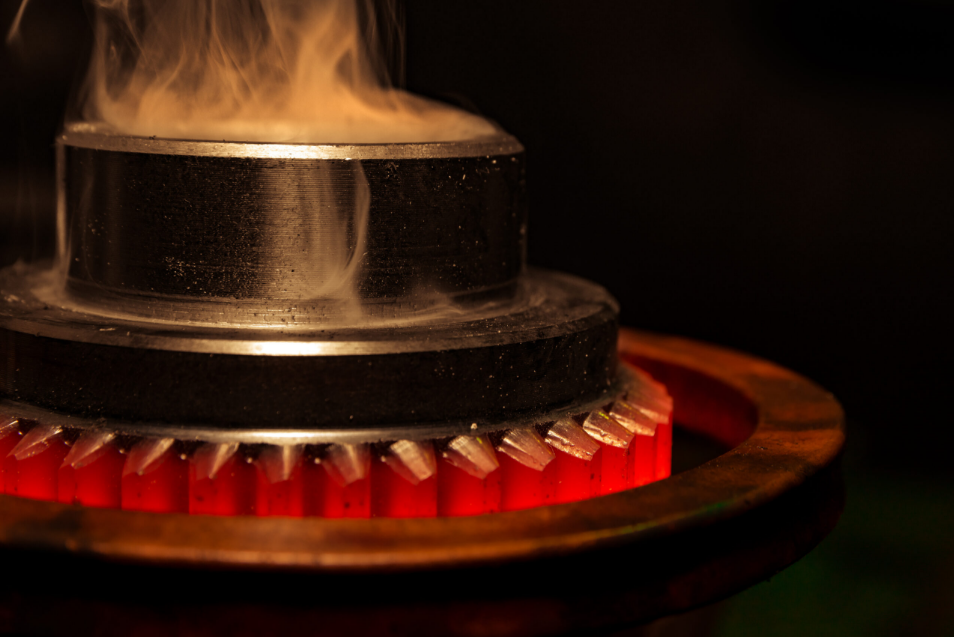
These processes can be tailored to meet specific requirements depending on the application and operational conditions of the gears.
The Key Heat Treatment Processes for Gears
1. Carburizing
Carburizing is a heat treatment process in which the gear surface is enriched with carbon at high temperatures, followed by quenching. The surface becomes much harder than the core, creating a high-carbon layer that enhances wear resistance and fatigue strength.
➡ Application in PairGears: At PairGears, we use carburizing for gears that require high surface hardness while maintaining a tough, ductile core. This is particularly beneficial for gears used in agricultural machinery and automotive systems, where high stress and wear resistance are crucial.
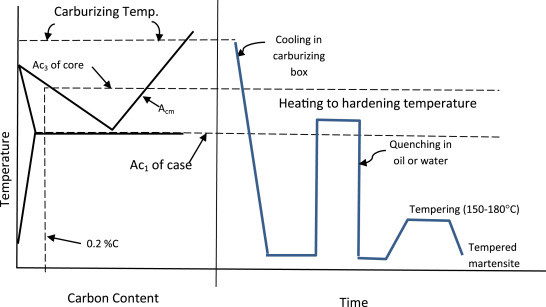
2. Nitriding
Nitriding involves introducing nitrogen into the surface of the gear at lower temperatures, typically between 500°C to 550°C. This creates a hard surface layer, improving wear resistance without the need for quenching. Nitriding also results in minimal distortion, making it ideal for gears with tight tolerances.
➡ PairGears Implementation: We employ nitriding for high-performance gears that need to resist corrosion and wear, especially in industrial machinery and trucks. This process ensures long-lasting, reliable performance even under extreme operational conditions.Explore our products here.
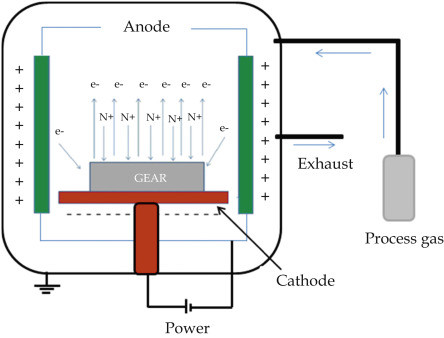
Induction hardening is a process where the gear is exposed to high-frequency electrical currents, which heat the surface. The gear is then rapidly cooled (quenched) to harden the surface, while the core remains relatively unaffected. This results in a hard outer layer and a tough inner core, making the gear ideal for applications involving heavy loads and impact.
➡ How PairGears Uses Induction Hardening: PairGears uses induction hardening for gears that need high surface hardness and resistance to abrasion, often used in construction machinery and automotive systems where the gears face repeated heavy-duty operations.
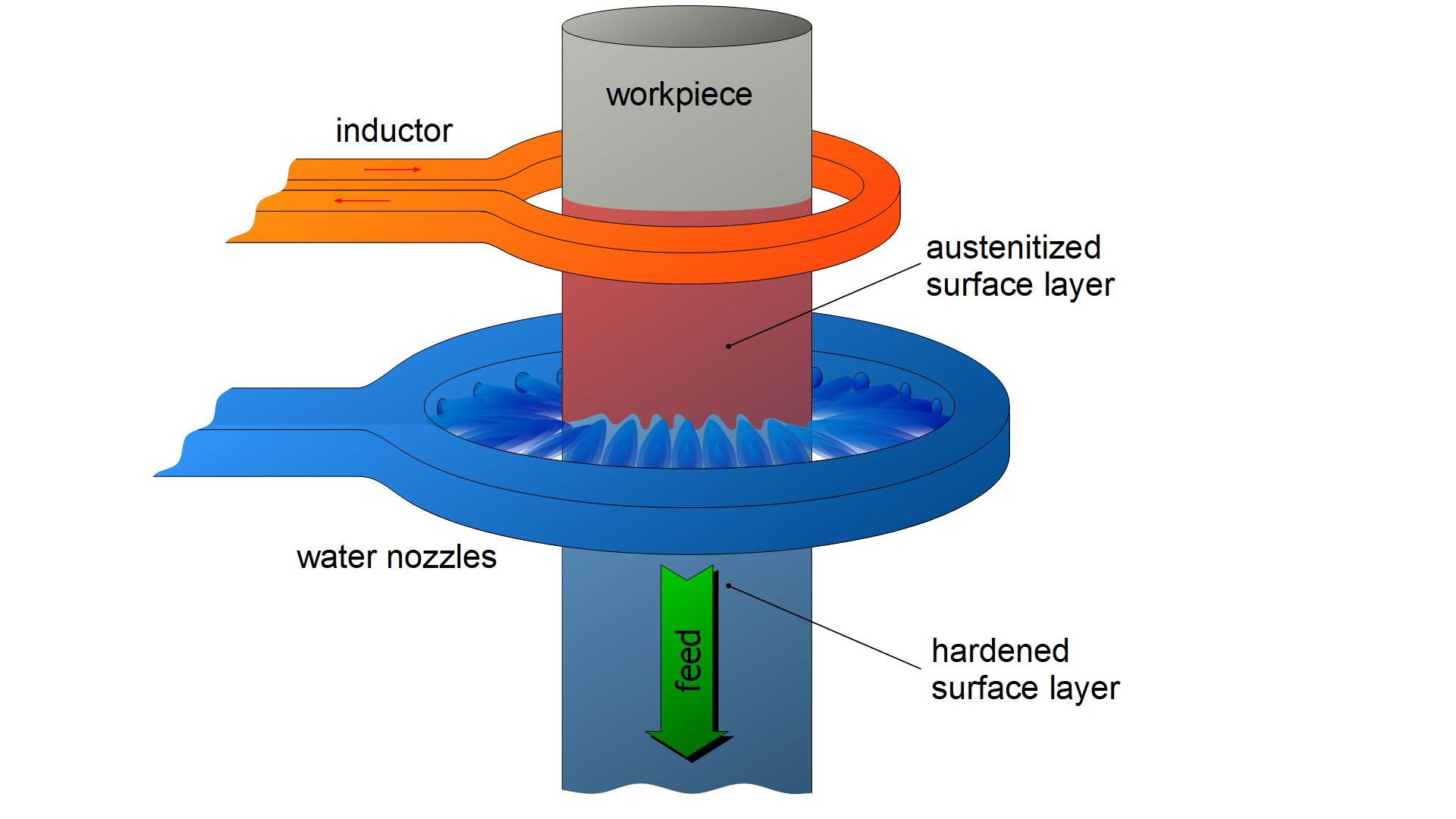
Quenching and tempering is a two-step process where gears are heated to a high temperature, then rapidly cooled (quenched) to achieve hardness. Afterward, the gears are tempered by reheating them at a lower temperature to relieve internal stresses and achieve the required balance between hardness and toughness.
➡ PairGears Approach: We utilize quenching and tempering for gears requiring a combination of high strength and toughness. This process is commonly applied in gearboxes and transmission systems, ensuring durability in long-term use.
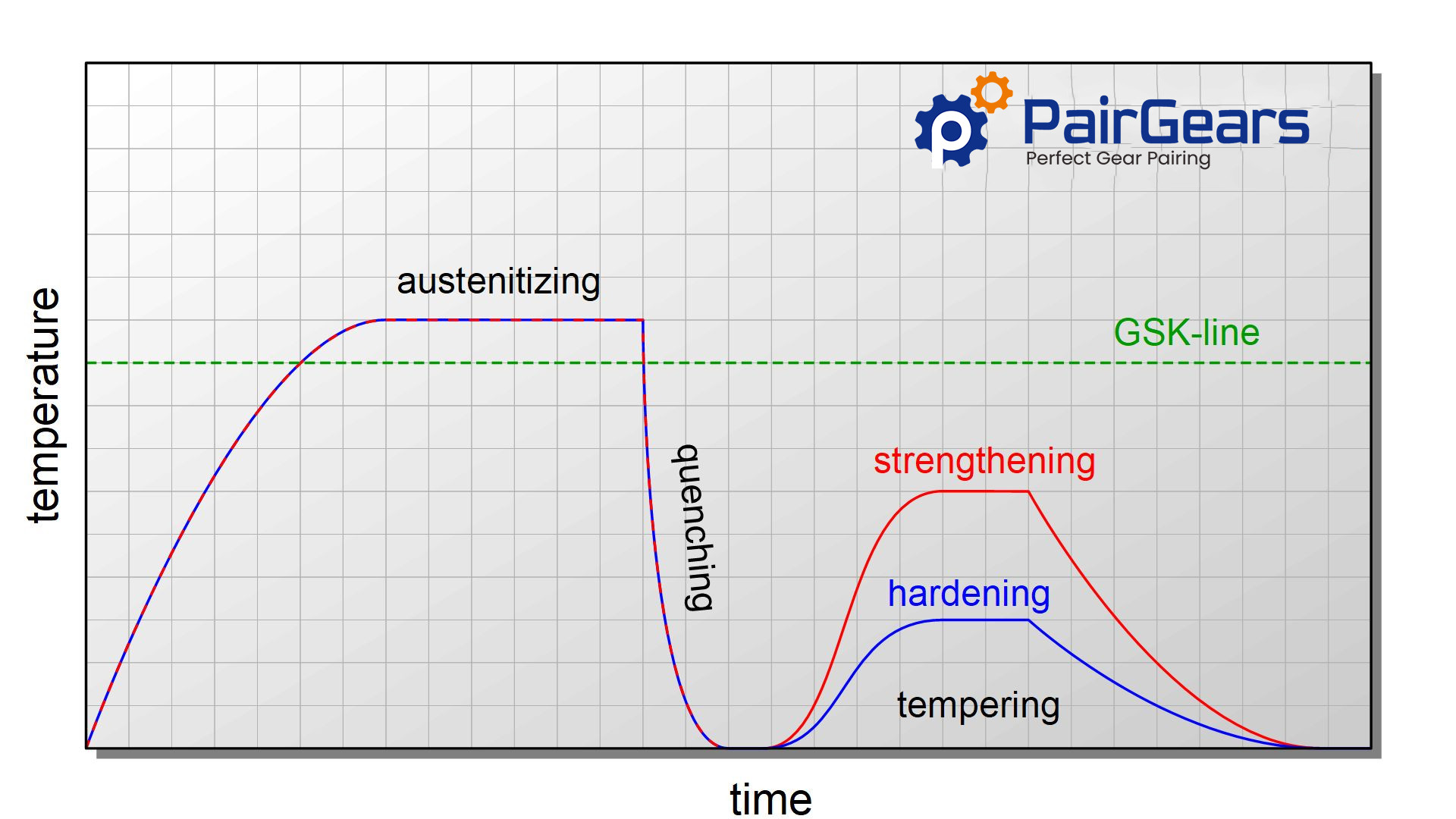
How Heat Treatment Enhances Gear Performance and Durability
Heat treatment plays a critical role in optimizing the mechanical properties of gears, improving their performance and durability in the following ways:
1. Increased Wear Resistance: Heat treatment creates a hardened surface that resists abrasion, ensuring the gears can handle continuous operation without significant wear.
2. Improved Fatigue Strength: The processes like carburizing and nitriding enhance the gear’s ability to withstand repeated loading, reducing the risk of fatigue failure.
3. Enhanced Toughness: Quenching and tempering processes provide gears with a balanced combination of hardness and toughness, making them more resilient to impact and shock loading.
4. Corrosion Resistance: Nitriding and other surface treatments can improve the corrosion resistance of gears, making them more suitable for harsh environments.
For industries such as automotive, agriculture, and industrial machinery, these enhancements ensure that gears perform optimally over a long service life, reducing downtime and maintenance costs.
PairGears: Delivering Superior Gears with Advanced Heat Treatment
At PairGears, we understand the importance of high-quality, durable gears in demanding applications. That’s why we invest in state-of-the-art heat treatment processes to ensure that each gear we produce meets the highest standards of performance and longevity. Whether you need gears for agricultural machinery, trucks, or industrial systems, our commitment to heat treatment excellence guarantees that you’ll receive gears that perform reliably in the toughest conditions.
For more insights on gear manufacturing, explore our product catalog or visit our precision manufacturing page.
Conclusion
Heat treatment is an indispensable part of the gear manufacturing process, enhancing the performance, wear resistance, and durability of gears. By leveraging techniques such as carburizing, nitriding, induction hardening, and quenching, PairGears ensures that our gears meet the rigorous demands of industries worldwide. With our advanced heat treatment processes, we are able to produce gears that provide long-lasting reliability, reducing maintenance and ensuring optimal performance.
Explore our products today and discover how PairGears can help meet your gear manufacturing needs.
Should you have any questions or require further assistance, please do not hesitate to contact our engineer: ben@pairgears.com.