Gear Manufacturing Process: Gear Shaping
- Share
- publisher
- pairgears
- Issue Time
- Jul 17,2024
Summary
Gear shaping is essential for precision and durability. This blog by PairGears explores gear shaping, its advantages, and its industry applications.
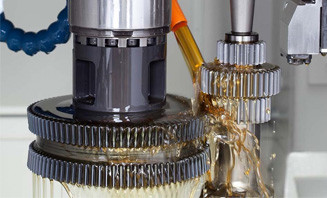
The Significance of Gear Shaping
In the realm of gear manufacturing, precision and reliability are essential. Gear shaping stands out as a cornerstone process in achieving these standards. At PairGears, we utilize advanced techniques to ensure our gears meet stringent quality requirements.
Understanding Gear Shaping
Gear shaping involves the use of specialized equipment to precisely cut gear teeth into a workpiece. Unlike other methods, gear shaping offers superior accuracy and surface finish, making it ideal for applications requiring smooth operation and minimal noise.
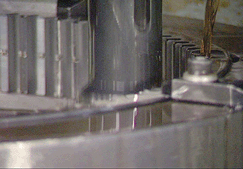
Advantages of Gear Shaping
1.Precision:
Ensures exact tooth profiles and spacing crucial for gear meshing and efficiency.
2.Efficiency:
Reduces manufacturing time without compromising quality.
3.Versatility:
Suitable for producing various gear types, including spur gears, helical gears, and internal gears.
Applications in Various Industries
Gear shaping finds extensive use in automotive, aerospace, and machinery manufacturing. Its ability to produce high-precision gears makes it indispensable in applications ranging from vehicle transmissions to industrial machinery.
Challenges and Things to Think About
Gear shaping has several benefits over conventional gear production techniques, but there are also some difficulties and factors to consider.
They consist of the following:
1.Tool wear:
The shaper cutter, a cutting tool used in gear shaping, can deteriorate over time and needs to be replaced on a regular basis. This may raise the price of the procedure overall.
2.Surface Finish:
Gear shaping can result in a high-quality surface finish, but it might be challenging to get the finish you want. Several variables, including the state of the cutting tool, the rate of cutting, and the caliber of the lubricant employed, have an impact on the surface finish.
3.Setup Time:
Compared to other gear manufacturing techniques, gear shaping may require a more extended setup period. The careful alignment and placement of the gear blank are necessary preconditions for the initiation of the cutting process.
4.Material selection:
The material used to make the gear might have an impact on how it is shaped. Some materials may not be suitable, while harder materials present more significant cutting challenges.

PairGears' Approach to Gear Shaping
At PairGears, we integrate cutting-edge gear shaping techniques with rigorous quality control measures. Our commitment to excellence ensures that each gear meets or exceeds customer expectations for performance and reliability.
Conclusion
Gear shaping plays a pivotal role in modern gear manufacturing, combining precision and efficiency to meet diverse industrial needs. PairGears continues to innovate in gear shaping technologies to deliver gears that drive innovation and reliability across industries.
If you want to learn more about gear shaping, you can visit the following pages:
Should you have any questions or require further assistance, please do not hesitate to contact our engineer ben@pairgears.com.