Gear Lubrication Methods: Benefits and Oil Types
- Share
- publisher
- pairgears
- Issue Time
- Oct 11,2024
Summary
Gear lubrication boosts performance, longevity, and reduces wear. Explore grease, splash, and oil circulation methods; choose right lubricants to minimize friction and prevent overheating.
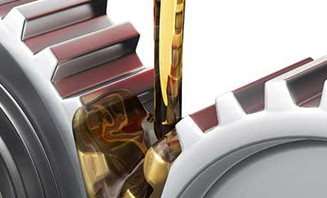
Introduction to Gear Lubrication
Lubrication plays a critical role in ensuring the smooth and efficient operation of gear systems, reducing wear and increasing lifespan. At PairGears, we understand the importance of using the right lubrication techniques to enhance gear performance, especially for agricultural machinery, trucks, and electric vehicles.
In this blog, we'll cover the most effective gear lubrication methods, the types of lubricants available, and how to select the right gear oil for your system. Each method has its benefits, and the right choice depends on the gear type, operating conditions, and your specific industrial needs.

Choosing the Right Gear Oil
Selecting the right lubricant for your gear system is essential. Here are the main factors to consider:
• Viscosity: Viscosity is the most critical characteristic of any lubricant. It impacts the lubricant's flow and how well it can protect gear surfaces under load.
• Additives: The additives used in the lubricant play a significant role in determining its properties, such as wear resistance, oxidation stability, and corrosion protection.
• Base Oil Type: The type of base oil (mineral, synthetic, or bio-based) should be chosen based on operating conditions, gear type, and other factors.
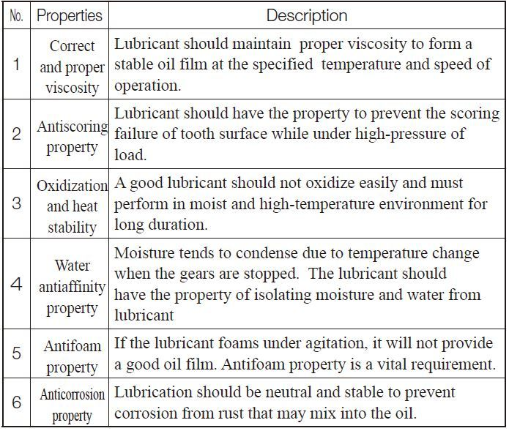
The properties that lubricant should possess
1、Viscosity
Choosing an appropriate viscosity grade is usually as simple as finding the recommendation in a component’s maintenance manual. Unfortunately, the manual does not always exist or the machine operates outside the conditions for which the OEM’s recommendations were made. Therefore, it is important to understand the methods for viscosity selection and the factors that affect the requirement.
The viscosity for a gear lubricant is primarily chosen to provide a desired film thickness between interacting surfaces at a given speed and load. Because it is difficult to determine the load for most viscosity selection methods, the load is assumed and the determining factor becomes speed.
One of the most common methods for determining viscosity is the ANSI (American National Standards Institute) and AGMA (American Gear Manufacturers Association) standard ANSI/AGMA 9005-E02. In this method, assumptions are made concerning the load, viscosity index and the pressure-viscosity coefficient of the lubricant.
The chart in Figure is applicable to spur, helical and beveled enclosed gear sets.To use this method, the type of gear set, gear geometry, operating temperature and the speed of the slow speed gear must be determined.
After calculating the pitch-line velocity of the slowest gear in the unit, the required viscosity grade can be read from the chart using the highest likely operating temperature of the unit.
It is important to note that this method assumes the viscosity temperature relationship of the lubricant (viscosity index = 90). If the VI of the lubricant deviates from this value, additional tables for oils with VI = 120 and 160 are included, or a viscosity-temperature plot can be used to interpolate the appropriate ISO viscosity grade.
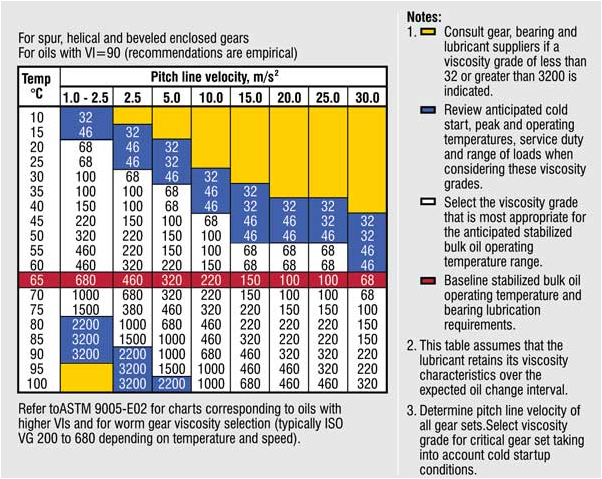
Although several common methods for gear lubricant viscosity grade selection are available, most should return similar values.
2、Gear Lubricant Type and Additive Selection
After selecting the viscosity grade, the basic type of lubricant must be chosen. While there are many variations, gear lubricants can generally be placed into three categories: R & O, antiscuff and compounded. The gear lubricant type that best fits a given application will be determined by the operating conditions.
Because there are no standard guidelines to help make this determination, the selection is somewhat subjective. Many equipment manufacturers will specify a viscosity requirement and leave this decision to the end user. Others will choose to be conservative and specify EP lubricants for the applications. It is therefore important to understand the general conditions that affect this requirement.
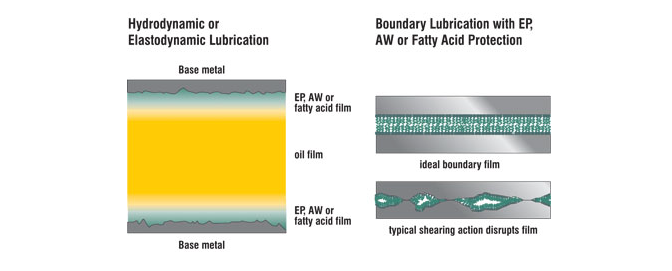
Three Main Gear Lubrication Methods
1. Grease Lubrication
Grease is used in both open and closed gear systems that operate at low speeds. Here are some critical points:
• Penetration Consistency: Choose grease with the right penetration for effective performance.
• Cooling Limitations: Grease doesn’t dissipate heat as effectively as oil, making it unsuitable for high-load, continuous operation.
• Over-lubrication Risks: Using too much grease can result in power loss due to churning and added friction. It’s essential to apply the correct amount to avoid these issues.
This method is best suited for gears operating at low speeds and loads, as it provides sufficient lubrication without requiring sophisticated equipment.
2. Splash Lubrication (Oil Bath Method)
Splash lubrication is commonly used in enclosed systems. The rotating gears splash oil onto the gears and bearings, requiring a minimum tangential speed of 3 m/s for effective lubrication. However, two issues need monitoring:
• Oil Level: If the oil level is too high, it causes excessive churning; too low, and it won’t adequately lubricate or cool the gears.
• Temperature Control: Friction can cause the system temperature to rise, which lowers oil viscosity and accelerates oil degradation. High-performance lubricants can withstand temperatures of up to 80°C to 90°C.
For systems with expected temperature surges, consider installing cooling mechanisms, such as heat sinks or fans.
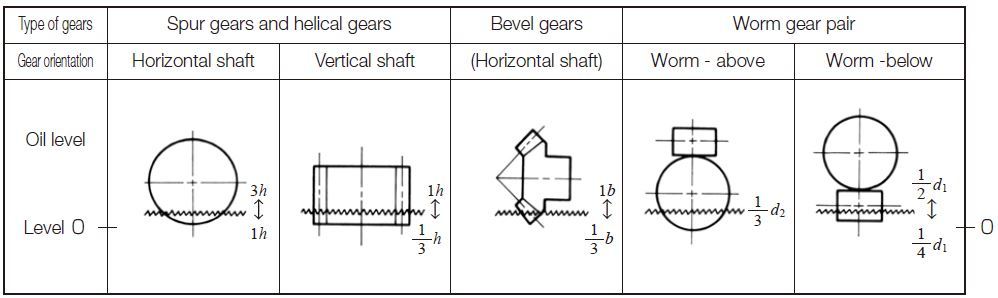
h = Tooth depth, b = Facewidth, d2 = Reference diameter of worm wheel, d1 = Reference diameter of worm
3. Forced Oil Circulation Lubrication
In this method, a pump applies the lubricant directly to the contact points of gear teeth, providing consistent and reliable lubrication. There are three common approaches:
• Drip Method: Lubricant is dripped directly onto gear contacts via a pump.
• Spray Method: Lubricant is sprayed directly on gear teeth for optimal coverage.
• Over-lubrication Risks: Using too much grease can result in power loss due to churning and added friction. It’s essential to apply the correct amount to avoid these issues.
While more complex, forced oil circulation offers superior cooling, cleanliness, and long-term performance, making it ideal for high-speed or large gearboxes. It also extends oil life by maintaining optimal viscosity and cleanliness.
The Benefits of Gear Lubrication
Proper gear lubrication offers numerous benefits, including:
• Reduced Friction:
Minimizes wear between gear teeth, preventing damage and reducing maintenance costs.• Heat Dissipation:
Helps prevent overheating, especially in high-load gear systems.• Corrosion Protection:
Lubricants contain additives that protect metal surfaces from rust and corrosion.• Extended Gear Life:
Proper lubrication increases the lifespan of your gears, ensuring continuous, efficient operation.For more information on how PairGears provides custom solutions for gear lubrication in agricultural and industrial machinery, visit our product page.
Conclusion
Choosing the right lubrication method and lubricant type is vital for optimal gear performance. Whether it's grease lubrication for low-speed applications or forced oil circulation for high-speed systems, each method has its advantages. At PairGears, we specialize in gear solutions tailored to your needs, ensuring durability and efficiency in every application.
Should you have any questions or require further assistance, please do not hesitate to contact our engineer: ben@pairgears.com.